|
(財)マイクロマシンセンターは参加企業や産総研とともに研究コンソーシアムを結成し、1991年から2000年までの10年間に亘り、約250億円の予算規模の「マイクロマシン技術研究開発プロジェクト」を推進しました。日本がコンセプトを生み出したマイクロマシンとは、数μm~数mm寸法の部品により構成された微小な機械のことです。本プロジェクトでは、将来いろいろな形でマイクロマシンが実用化されることを期待して、マイクロマシン実現に資する技術的なプラットフォームづくりを目指しました。
本プロジェクト発足当時は、半導体など通商面での貿易摩擦や、基礎研究ただ乗りの批判がわが国に向けられていました。日本として独創的な研究開発が求められるなか、本プロジェクトは、諸外国に例を見ない新しい概念の研究プロジェクトとしてスタートしました。当初(第Ⅰ期)は技術課題を抽出するために、「ミクロの決死圏」のようなマシンを想定して要素技術の開発に取り組みました。後半の第Ⅱ期では、これらの要素技術をマシンシステムに統合するためのシステム化技術の研究に邁進しました。この新発想のプロジェクトは海外からの関心も高く、また海外からの調査団やメディアを通じて外部に広く伝えられました。
この結果、特許出願が530件、学会等への発表が約1,500件など目を見張る成果を上げました。、本プロジェクトによって培われた微細加工技術やセンサー技術、システム化技術などのマイクロマシン技術は、各企業の技術力を高め、その後のMEMS産業をはじめとする関連産業の発展に大きく貢献したといえます。 |
当初の5年(第Ⅰ期)は技術課題を抽出するために、「ミクロの決死圏」のようなマイクロマシン(数μm~数mm寸法の部品により構成された微小な機械のことで我が国発のコンセプト)を想定して要素技術の開発に取り組み、後半の5年(第Ⅱ期)では、これらの要素技術をマシンシステムに統合するためのシステム化技術の研究を行いました。
すなわち本プロジェクトでは、将来いろいろな応用分野においてマイクロマシンが実用化されることを期待し、基盤技術、デバイス技術およびシステム化技術を蓄積したマイクロマシン実現に資する技術的なプラットフォームづくりを目指しました。 |
財団法人マイクロマシンセンター (→ 全体とりまとめ) |
(株)アイシン・コスモス研究所 |
ファナック(株) |
オムロン(株) |
(株)フジクラ |
オリンパス(株) |
富士電機(株) |
川崎重工(株) |
松下電器産業(株)
(当時;現在のパナソニック(株)) |
三洋電機(株) |
三菱重工(株) |
住友電気工業(株) |
三菱電機(株) |
セイコーインスツルメント(株)
(当時;現在のセイコーインスツル(株)) |
三菱電線工業(株) |
テルモ(株) |
三菱マテリアル(株) |
(財)電気安全環境研究所 |
(株)村田製作所 |
(株)デンソー |
(株)安川電機 |
(株)東芝 |
横河電機(株) |
(財)発電設備技術検査協会 |
Royal Melbourne Institute of Technology |
(株)日立製作所 |
SRI International |
工業技術院 機械技術研究所、電子技術総合研究所および計量研究所
(当時;現在はいずれも(独)産業技術総合技術研究所に統合) |
■第Ⅰ期では想定システムの構成に必要な微小機能要素技術、トータルシステム等について幅広く研究開発を行いました。 |
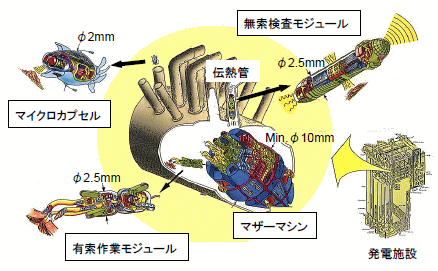 |
第Ⅰ 期における開発項目と開発目標 |
開発項目 |
研究開発目標 |
微小機能要素技術 |
マイクロマシンの知能、環境認識機能、移動・推進機能、作業機能等の発現に必要な、IC の高密度実装化、センサー(視覚、触覚等)、および力、運動伝達機構のマイクロ化及び高機能化を図り、マイクロマシンの機能要素技術を確立する。機能要素の大きさは、数10mm
から数mm 程度の大きさとする。 |
エネルギー供給技術 |
マイクロマシンへのエネルギーの外部供給法(光ファイバー等)および内部供給法(化学電池等)について、マイクロ化及び高効率化を図り、マイクロマシンのエネルギー供給技術を確立する。 |
システム制御技術 |
マイクロマシンの制御に必要な情報処理技術、通信技術、分散協調制御技術及び外部の人間とのインターフェイス技術等を開発し、マイクロマシンの制御技術を確立する。 |
評価技術 |
マイクロマシンを構成する微小機能要素の特性等を計測・観測し、評価する技術を確立する。 |
■第Ⅱ期では、前期トータルシステムの調査に基づき中間見直しを行いました。すなわち、よりニーズに合ったシステムを想定し直し、これらの想定システムの実現に必要かつ可能性のある機能デバイスを選定して、こうした機能デバイスの高度化(マイクロ化、高機能化)技術、及びシステム化技術について研究開発を行いました。 |
|
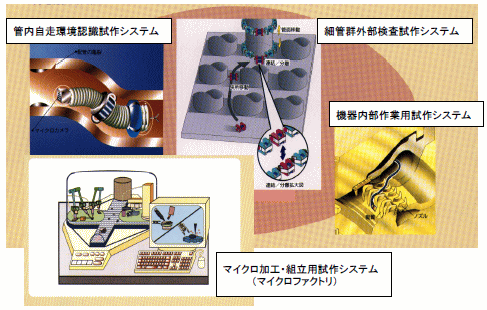 |
第Ⅱ期における開発項目と開発目標 |
開発項目 |
研究開発目標 |
システム化技術 |
・複雑な機器の狭小部に用いることを想定した管内自走環境認識用、細管群外部検査用及び機器内部作業用試作システム、及び小型工業部品の生産に用いることを想定したマイクロ加工・組立用試作システムの製作を通じたエネルギー供給技術、設計
・製作技術等のシステム化技術の開発・個々の機能デバイスの統合、マイクロ化、高性能化による試作システムへの実装化技術の開発 |
機能デバイスの高度化技術 |
・駆動技術である人工筋肉,連結技術であるマイクロジョイント、極低摩擦サスペンション、エネルギー技術であるマイクロバッテリ等の先進的な機能デバイスのマイクロ化、高性能化を図る技術の開発
・センサ、レーザを複合化したマイクロレーザカテーテルの技術の開発
・センサ、能動湾曲機能を複合化したマイクロセンサカテーテルの技術の開発 |
共通基盤技術 |
・マイクロマシン群制御技術の開発
・力、トルク等の計測技術の開発
・微小機能要素等の評価技術の開発 |
総合調査研究 |
・マイクロマシンシステム技術のトータルシステム像と将来の展開の明確化を図る。 |
■第Ⅰ期と第Ⅱ期を通じて、マイクロマシン技術の体系化に必要な主要技術について網羅的に研究開発を行い、技術的なプラットフォームづくりを目指しました。 |
|
|
第Ⅱ期では、4つの試作システムについてシステム化技術の研究開発を行いました。これらの試作システムに関する主な成果(トピックス)は以下の通り。 |
(1)管内自走環境認識用試作システム
参加企業:デンソー、三洋電機、東芝 |
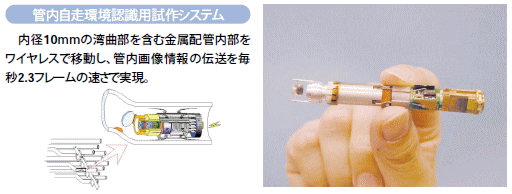 |
(2)細管群外部検査用試作システム
参加企業:三菱電機、松下電器、住友電気工業 |
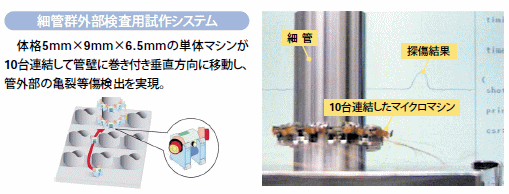 |
(3)機器内部作業用試作システム
参加企業:オリンパス、村田製作所、オムロン |
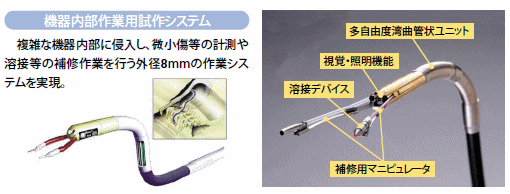 |
(4)マイクロファクトリ
参加企業:SII、ファナック、日立、アイシン、安川電機、富士総研、三菱電機 |
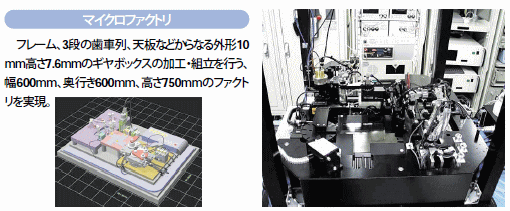 |
|
|
(1) 加工・組立技術
マイクロな部品の加工では、大きな部品では問題にならない結晶粒界の影響を受けたり、部品の組立では組立の位置決め精度と部品寸法の比が変わらなくなる等、従来の技術では対応できないことが多く、プロジェクトでは新規な加工・組立技術を開発している。
マイクロ電解加工技術(セイコー電子)
マイクロ部品を加工する場合、部品寸法が小さくなればなるほど高い加工精度が要求される。このため、STM(走査型トンネル顕微鏡)を利用した湿式3
次元電解加工を開発した。加工物に機械的な力や、熱応力がかからない加工方法で、電気化学的に局所的な加工を行い、3 次元的な微細な形状の加工ができる特徴を持っている。現在0.2
ミクロンの加工精度を得ている。
セラミック微細加工技術(住友電工)
LIGAプロセスは強力なX 線を用いた微細構造体の転写技術で、プロジェクトでは弧の技術により電圧複合体を作るための高さ120 ミクロンのPZT
セラミクスの柱状構造体を作製した。X 線でパターニングしたレジスト構造体にスラリー状のセラミクスを注入し、レジストを焼きとばすことで構造体を得ている。
異種材料直接接合技術(日本電装)
通常の機械部品の組立は、ネジ、接着剤等で行なわれるが、機械が微小化するとそれよりも微小なサイズのネジ自体の製造が困難になると共に、接着剤等による接合では、接着層による寸法誤差が無視し得ないレベルとなってしまう。また、微小部品より小さな接着剤を塗布する事さえ難しくなってくる。このため、プロジェクト中では、水の分子をイオン化させて接合したい材料表面に照射した後、材料同士を専用の把持装置ではさみこんで加圧・加熱することによって、水素結合のみで直接接合する接着剤の不要な接合技術の開発を行なっている。これまで、シリコン(回路等)とアルミニウム(構造体)、圧電体(アクチュエータ)とアルミニウムなどの接合を原子レベルで実現している。
金属粉体射出成形技術(オリンパス)
マイクロマシンの構成部品の製作においても、同一形状の部品を大量に作製することが必要である。このため、機械加工技術を使わず、マイクロで複雑形状の金属部品を大量に作る射出生計技術を開発し、多自由度マニピュレータの構造体となる外径1mm
の管状構造体を試作した。
複合超精密マイクロ加工(ファナック)
マイクロマシンでは小型で3 次元複雑形状の部品を加工する必要がある。このため、超精密加工用のダイヤモンドエンドミル、高精度スピンドル、工具ホルダ等の開発により表面精度58nmRmax
を達成した。写真は3 次元の曲面の加工例。
シェルボディ形成技術(日本電装)
マイクロマシンはあらゆる環境で動作することが要求され、そのため環境からアクチュエータ、回路等を保護するボディが必要とされる。このため、メッキによる金属膜を用いたシェルボディ形成技術を開発した。複雑な3
次元形状のボディも形成することが可能で、機能集積のための電気配線を内臓することもできる。
3次元マイクロ部品加工(松下技研)
マイクロマシンの加工では、加工物が小さいため従来の加工より高い寸法精度、平滑な表面が求められる。このため、微細放電加工技術と、面粗さの高精度化を目的としたアルミネの微粒子を混入させた電解高仕上げ面河口技術の開発により、表面粗さ32nmRmax
を達成した。
円筒積層プロセス―組立技術(松下技研)
マイクロマシンの組立は、部品が小さくなるため、そのハンドリング、組立は非常に難しい。このため、組立なしでモータを作製できる円筒積層プロセスを開発した。この方法は、回転するロータ(円筒)表面にロータ電極、絶縁層、犠牲層、ステータ電極を積創始、配線・ケーシングを行なったあと犠牲層を除去するもので、組立工程なしでサブミリサイズのモータが作製できる。
(2)センサ
移動して検査を行うマイクロマシンや、微小な部品を加工組立するマイクロファクトリ、生体内で治療・診断を行なうマイクロカテーテルでは、環境を認識する各種のセンサが必要とされ、従来のセンサよりも小型で低消費電力が要求されている。
マイクロジャイロ(村田製作所)
移動するマイクロマシンでは、マイクロマシンの姿勢を検知する必要がある。このため、半導体プロセスを駆使して小型で高性能の振動型ジャイロを開発した。多結晶シリコンの構造体を振動させ、角速度変化で生じるコリオリ力を静電容量変化として検出するもので、小型ながら実用レベルの2度/sec
の分解能を得た。
光スキャナ(オムロン)
ワイヤレスで検査情報を送信するマイクロマシンでは、消費電力、情報処理力に制限を受けるため、原理的に単純な物体検出方式が求められる。このため、レーザ光を走査し、反射光を検知して物体を認識するセンサを開発した。レーザ光源、光のスキャナ、受光素子が一体化することにより小型化を達成した。受光素子、光スキャナを同一10mm
角のシリコン基板上に集積化を行った。
マイクロ光分析(横河電機)
配管内の検査用マイクロマシンに装備され、配管内の付着物の元素分析を行うセンサ。物質から放射される光の分光器と検出部から構成されている。検出部となるショートキーバリアダイオードをFIB
により微細加工し、赤外光の検出に成功した。
CCD マイクロカメラ(東芝)
人が入れない場所で高度な検査を行うマイクロマシンでは、カラーで動画情報を送信できる小型のCCD が要求されている。このため、CCD イメージセンサ、CCD
のドライバ回路、画像処理回路を一体化した3 次元実装マイクロCCD の開発を行い、管壁等40 万画素相当の分解能で目視検査が可能で、微小雲台機構により任意方向の検査ができる直径10mm
のCCD マイクロカメラの開発に成功した。
光学式圧覚センサー医療(オリンパス)
生体内で治療・診断を行うマイクロカテーテルにおいて、施術中のカテーテル先端の欠陥内壁への接触押圧状況を検出するマイクロ圧覚・触角センサが切望されている。このため、小型化のため面発光レーザを使用し、微弱な接触圧に対しても検出可能な光学式の圧覚センサを開発した。サイズは1.8x1.4x0.65
と小型で、1mN の検出感度を得た。
イメージファイバスコープ(三菱電線)
狭隘部の検査を行うマイクロマシンや、微小な部品を加工組立するマイクロファクトリ、生体内で治療・診断を行うマイクロカテーテルでは、検査部位近づき詳細検査を行う小型のセンサが必要である。このため、外径が小さくフレキシブルで狭隘部を通過して検査部に到達できるイメージファイバスコープを開発した。外径は200
ミクロンと世界最小で、照明用のライトガイド、2000 本もの画素ファイバを細径化技術により達成した。
(3)マイクロ機構
マイクロマシンを移動させたり、作業等を行うマニピュレータを動かすためには非常に小さなアクチュエータや効率良く力を伝達するマイクロ機構が必要となる。プロジェクトでは、様々なマイクロマシンの種々の用途にあった、直線的な動きをするアクチュエータと回転するモータ及びマイクロ機構の研究開発を行っている。マイクロ機構では大きなものでは問題にならない摩擦や熱の問題が発生するため、マイクロ特有の機構が必要である。
(3-1)リニアアクチュエータ
静電リニアアクチュエータ(富士電機総研)
マイクロファクトリにおける微小部品の搬送等においては、余り力を必要としないが小型で大きな変位を持つアクチュエータは、これまで変位が小さい問題があったが、新規な変位拡大機構の開発により、小型で摩擦がない大きい変位の静電リニアアクチュエータを開発した。動作は制御により、前後駆動、ロック、フリーの動作モードが可能。
形状記憶合金(SMA)マイクロコイルアクチュエータ(三菱電線)
生体内で治療・診断を行うマイクロカテーテル等の首振りを行うためには、小型で単位断面積当たりの発生力が大きく、変位も大きなアクチュエータが要求される。このため、難加工材料の形状記憶合金をコイル状(線径30
ミクロン、コイル外径100 ミクロン)に加工した。このコイルは形状回復力50mN の能力があり、レーザの照射により駆動する方式により体内で使用するカテーテルを安全に首振り運動させることができる。
人工筋肉(SRI インターナショナル)
圧電体よりも変位が大きく、形状記憶合金よりも発生力の大きな電歪ポリマーを開発した。電圧の印可により最大32%変位する。大変位、中発生力の動力源に向く。
(3-2) モータ
電磁モータ(富士電機総研)
マイクロマシンにおいて力を必要とする作業等に用いるアクチュエータとして体積当たりの発生力の大きなアクチュエータが必要である。このため、高効率で高出力が取り出せる電磁タイプのモータを開発した。スパッタリングによる薄膜磁石形成技術と半導体技術を駆使した4
層でコイル占積率の大きな薄膜多層コイル技術の開発により直径1mm、高さ2mm のモータを開発した。
静電マイクロアクチュエータ(安川電機)
マニピュレータの先端に取り付くモータ等には非常に小型のモータが要求される。マイクロになるほど表面積/体積の比が大きくなるので、静電力はマイクロなほど有利となる。直径およそ1mm
以下のモータでは電磁タイプよりも効率、出力とも静電モータの方が優れることを明らかにした。現在までに直径5mm の静電モータの開発に成功した。
マイクロ圧電モータ(セイコー電子)
マニピュレータの継ぎ手の駆動等では減速機構のいらない低回転で高トルクのモータが要求される。このため、複数の圧電体でロータを叩いて回転させるタイプで高出力が得られるマイクロ圧電モータを開発した。機構的にロータとステータが、常時接触する方式なので、電源がOff
の状態では固定となるので、アームの継ぎ手などに適することがわかった。現在外径2mm のモータの開発に成功している。
(3-3) マイクロ機構
伸縮屈曲アクチュエータ(日本電装)
曲がった配管内を移動するマイクロマシンでは、小型で屈曲変位するアクチュエータが必要である。このため、一つのアクチュエータで伸縮、屈曲動作をする全く新規な構造のアクチュエータを開発した。3分割した電極を設けた圧電ユニモルフを積層した構造で、わずか4本の配線で3次元的に屈曲変位を行なわせることができる。
管状マイクロマニピュレータ(オリンパス)
狭隘部の検査を行うマイクロマシンや、生体内で診断・治療を行うマニピュレータでは変形の自由度が高く、外径の細いマニピュレータが必要である。このため、薄板形状記憶合金(SMA)アクチュエータ、SMA
の制御回路、センサ等を薄いフィルムに集積化した多機能フィルム技術等の開発により直径1mm、5 自由度の変形が可能なマイクロマニピュレータを実現した。マニピュレータは管状(中空構造)となっており、内部に検査のためのファイバスコープ、センサ、配線等が内臓できる。
マイクロ検査マシン(日本電装)
曲がった配管内を移動し、配管のクラック等を検査するマイクロマシンを開発した。このシステムはアクチュエータと放熱体を直接接合する技術、ごみ等外界からマイクロマシンを保護するジェルボディ形成技術を新たに開発することにより実現した。直径5.5mm、全長20mm、重さ1g
と小型ながら、毎秒6mm の速度で曲がった配管内を移動し、配管のわずか数ミクロンの亀裂を検知できる。
(3-4) ポンプ
高出力マイクロポンプ(日立製作所)
作業を行うマイクロマシンの油圧源として、発熱の問題があるマイクロマシンの冷却水循環用ポンプとして、小型で高出力のポンプが必要である。このため、精密微細加工技術、部品の直接接合技術により、直径7mm
のマイクロポンプを試作した。小型ながら10 気圧以上の圧力を発生した。
光駆動マイクロポンプ(アイシンコスモス)
マイクロファクトリにおけるマイクロ部品の接着組立では、マイクロ部品よりも小さな接着剤を塗布する非常に微量の液体を定量的に吐出するポンプが必要である。このため、半導体プロセスによりシリコンダイアフラムをレーザ光の照射で駆動する4x15mm
のマイクロポンプを試作した。電気を用いず光だけで駆動するため、電気が使用できない体内や、電磁波干渉を受ける場所での流体の駆動ができ、25nl
の微小容量の液体を精度よく吐出できる。
(4)エネルギー供給
マイクロマシンに電線でエネルギーを供給する場合、電線(ワイヤ)の硬さがマイクロマシンの動作を妨げるため、ワイヤレスでのエネルギー供給が強く要望されている。
マイクロ発電機(三菱電機)
配管内の水流でタービンを回転させ発電を行う、マイクロ発電機の開発を行った。円筒面への薄膜磁石形成技術、効率向上のための円筒型高密度巻線固定子技術、高速回転を可能にする高速マイクロ軸受け技術の開発により直径1.2mm
の発電機を思索に成功した。
マイクロ波エネルギー供給(日本電装)
高いエネルギーが伝送でき、配管内や電波シールドした空間内で有効なエネルギー供給方法として、電波を用いてエネルギー供給を行う、マイクロ波エネルギー供給システムの開発を行った。システムはマイクロ波を効率良く受信するアンテナと高周波を直流に変換する高周波、高耐圧のダイオードの開発により、受信効率90%を達成した。
マイクロ光電変換デバイス(テルモ)
人工臓器等体内に埋め込む医療機器に対して、その動作に必要なエネルギーを外部からワイヤレスで供給する場合には、人体への負担が少ないようできる限り小型で、しかも、人体に影響を与えないエネルギー供給が望まれており、経皮的に光を供給する光電変換デバイスの開発を行った。レーザ光で高効率に発電するフォトセルと必要な電圧にまで昇圧する小型のトランスの開発により実現した。
曲面実装光電変換デバイス(三洋電機)
検査を行い、その情報を通信する様な多機能のマイクロマシンでは、多くの電子回路、センサなどのデバイスを駆動することとなる。この場合、複数のデバイスに多くの電流を供給するには、できるだけ広い面積に光電変換デバイスを装着することが望まれる。そのため、作製プロセスを改良し、フレキシブルな基板に光電変換素子を形成する技術により、マイクロマシンの形状を変えずにエネルギー供給面積を広くし、小型で、高出力のエネルギー供給が可能な曲面実装光電変換デバイスの開発を行った。
高電圧光電変換デバイス(三洋電機)
自走したり、作業等を行うマイクロマシンでは、高出力の静電、圧電アクチュエータに電力を供給する必要がある。これらのアクチュエータの駆動には、高電圧(~数百V)、小電流の電力が必要で、バッテリーや従来の光電変換デバイスでは駆動できない問題があった。そのため、微細な光電変換デバイスを小さい面積に非常に数多く直列に接続する技術により、小型で、高電圧を発生するデバイスを開発した。10mm
角のデバイスで207V を発生する、世界最高電圧の光電変換デバイスの開発に成功した。
マイクロバッテリ(三菱マテリアル)
自走したり、作業等を行うマイクロマシンにおいて光が届かない場合等電力が供給できないときの駆動用電源として、小型で高容量のバッテリが必要である。このため、電極の薄膜化、膜状電極形成技術の開発により、充放電可能な直径5mm、高さ1.5mm
のニッケル水素マイクロバッテリを開発した。従来のミニチュア電池に比べ一桁高容量化に成功した。
(5)制御
小さくても、移動・検査などを行うマイクロマシンではアクチュエータ、センサを制御する回路が必要となるが、従来の制御回路をそのまま小さくすることは非常に困難がある。それは、現状でも、制御回路は十分集積化が進んでいること、また、集積化により同じ発熱量でも回路が高温になる問題が生じるからであつ。このため、プロジェクトでは回路が小さな制御方法などの研究開発を行っている。
行動型制御(IS ロボティクス)
マイクロマシンのための制御方法として動作部にセンサを配し自律制御を行い、全体の制御回路・駆動回路の小型化を可能にする行動型制御アルゴリズムを用いた外部配管用検査ロボットを開発した。わずかに3つの8
ビットマイクロプロセッサと64k バイトのプログラムという小型の制御ながら、ロボットは4 自由度で制御することが可能で、2つのグリッパで配管を交互に把持しながら配管上の3
次元的な移動ができる。
変態制御(三菱重工)
ホロンの接続状態を群制御することにより、形態を変え、移動することができるホロニックメガニズムの変態制御の研究を行った。
(6)通信
通信制御(メイテック)
配管内で検査等を行うマイクロマシンでは、検査情報を外部に送ったり、制御情報を外部から送信するため通信が必要とされる。低消費電力で通信機構が非常に小型のマイクロマシン特有の壁面振動通信技術の研究を行っている。現在、圧電体で管壁を叩き、19.2kbps
の伝送速度でカラー静止画像の情報が送れることを確認した。
(7)計測
プロジェクトでは種々のアクチュエータ等を開発しているが、それらの発生する力や回転トルクを正確に計測する手法はない。また、3 次元的加工されたマイクロ部品の形状を正確に計測する手法もないため、マイクロな領域における種々の計測技術を開発する必要がある。
微小回転トルク測定装置(安川電機)
マイクロモータの開発において、特性の改善等を行うためにもマイクロモータの出力(トルク)を計測する技術は必要不可欠である。しかしこれまでは10-5Nm
以下のトルクを測定できる装置はなかった。このため、トルク伝達部に空気軸受けを使用したトルクロスのない機構、測定物に非接触で負荷をかける機構、高分解能荷重変換器の使用により10-7Nm
の微小トルクを計測できる計測装置を開発した。
(8)その他
メンテナンスシステムの研究(発電技研)
人が入れない場所で検査、補修を行うマイクロマシンの特長が活かせる発電施設におけるマイクロマシンのニーズを幅広く調査し、発電施設の保全作業に適したメンテナンス用マイクロマシンの概念を構築した。 |
 |
|
マイクロマシン技術研究開発プロジェクト(1991-2000年)の成果や波及効果を評価するため、NEDOはプロジェクト終了後5~6年経過した時点で詳細なアウトカム調査(マイクロマシン技術に係るアウトカム調査(2007年3月))を行いました。以下は、本調査による記述になります。 |
本プロジェクトの開発成果は、大きく分けて「要素技術開発」、「システム化技術開発」及び「これら技術の体系化」に関与している。
この中で、マイクロマシン技術の体系化に挑戦したことは高く評価できるものの、実用的な視野からまとまった成果があったとは評価し難い。この原因は多分に、技術の体系化には当該分野の広範な技術そのものがある程度成熟した段階で可能なものであることに拠っており、今回のように、発展途上の技術に、しかも新規産業創出型産業科学研究開発制度の主旨にかなうような形での体系化を目指すことは、極めて困難であったと言わざるを得ない。
一方、「要素技術開発」、「システム化技術開発」においては、世界初ないし世界最高水準の開発成果が数多く得られている。その意味では本プロジェクトは十分成功したものであると断定される。もちろん、世界最高水準のアウトプットが即アウトカムに繋がるものではないが、プロジェクト終了後5年を経過した現時点では、後章で述べるように、本プロジェクトの波及効果は膨大なものがあり、「マイクロマシン技術」はまさに21
世紀のわが国の産業基盤を支える技術分野として育成されつつあると言える。
研究開発項目毎の評価は仔細に過ぎるので、総括的な評価になるが、
1)管内自走認識用試作システムでは、直径14mmφの小型マシンを無索で管内走行させ、駆動エネルギーと同時に管内環境情報の授受の可能性を実証した点で、世界最高水準の成果といえる。
2)細管群外部検査用システムにおいては、多数のマイクロマシンを自在に連結・分離し、システマテックな作業行動を実現する道を開いた点も、世界初で評価できる。
3)機器内部作業用試作システムでは、将来、複雑・狭隘な機器内部のモニタリング、溶接補修作業等が遠隔操作で可能になることを証明した点で、化学プラント分野や医療分野において、早期に実用化が期待できる成果を含むものとして評価できる。
4)マイクロ加工・組立用試作システムは、マイクロファクトリシステムを想定した技術開発であり、既に多数の公私のファンドリーファームが稼動しており、DTF(Desk Top Factory)研究会(長野県諏訪地方で27
企業・団体が参加)の活動のような動きもあり、最も実用化に近接した技術成果をあげたと言える。
5)機能デバイスの高度化技術については、多数の研究サブ項目があり一概に論じられないが、人口筋肉の研究や自由関節デバイス、マイクロカテーテル、マイクロ触覚センサ等、今日のマイクロマシンの医療分野への進展の基礎となりうる技術開発がなされたことは優れた成果である。
6)共通基盤技術についても、多数の研究サブ項目があるが、それぞれに高度な成果を得ている。特にマイクロマシンのような新規な製品を作った場合、それらの機能・品質、さらには安全性等の評価技術が伴わないと実用化・汎用化に繋がらないが、その面の研究も着実に成果を得ている点が評価できる。
7)総合調査研究は、本プロジェクトのように、当初、比較的基礎的な要素技術の開発からスタートし、途中で実用化を意識したシステム化開発に目標を切替えたこと、しかも関係実施機関が非常に多数であり、錯綜する開発進行管理を成功裏に達成し、今日の新規産業基盤の一つと呼ばれるまでに纏め上げた成果も大きなものである。 |
総じて、本プロジェクトの開発技術を評価するならば、先の「評価報告書」にあるように、「計画と比較した達成度は、要素技術については高く評価できるが、『マイクロマシン技術の統合的体系化』の観点からは時期尚早の感もあり不十分である。要素技術については、今後実用化にいたる可能性が高く、波及効果も期待できる。」に尽きると思われる |
(マイクロマシン技術に係るアウトカム調査(2007年3月)からの抜粋) |
|
|
|